Weld and Safety Wake-Up Calls in Australia
- Karen Black
- May 16
- 6 min read

A mate of mine — let's call him Sam — thought welding accidents only happen to the blokes who cut corners. Not him. He was smart. Careful. Until the day his regulator failed and a fireball took half his arm with it. That day changed more than just his job. It changed how I think about weld and safet too.
Thing is — Sam's story isn't rare. In fact, it's barely a ripple in the sea of near-misses and tragedies that happen across Australia's workshops every year. The difference? His made it to the hospital. Some don't. And most — aren't even reported. I watched as Sam struggled through rehab, as he tried to hold a coffee cup with his new prosthetic, as he explained to his kids why dad couldn't pick them up anymore. And all because of what? A $50 part that needed replacing? Five extra seconds to check connections? A proper welding mask that might've at least protected his face?
The worst part wasn't the accident. It was knowing it was completely preventable.

It Still Happens — Welding
Accidents in Australia
Common Incident Types That Change Lives Forever
The following scenarios represent composite examples based on incident types regularly documented by Australian workplace safety authorities. While specific details have been adjusted, these reflect the patterns and causes of real welding accidents that occur in Australian workplaces.
Electrocution Risk in Rural Settings
Scenario: A contractor in his 40s electrocuted while MIG welding on metal equipment in an agricultural setting
Common failures: Faulty earth lead connections, absence of voltage reduction devices, worn insulation on older equipment
Prevention measures: Regular equipment checks, proper earthing, mandatory use of VRDs
The lesson: Electricity doesn't give second chances. Inspect before every job.
Gas-Related Explosions in Automotive Workshops
Scenario: Apprentices suffering burns when gas leaks from damaged hoses ignite in confined spaces
Common failures: Missing flashback arrestors, improper cylinder storage, inadequate pre-start checks
Prevention measures: Proper hose inspection protocols, flashback arrestors on all equipment, secure upright cylinder storage
The lesson: Gas management isn't optional — it's critical to staying alive.
Long-Term Respiratory Damage
Scenario: Experienced welders diagnosed with occupational asthma or other lung conditions after decades in the trade
Common failures: Inadequate ventilation systems, lack of respiratory protection, work on galvanized or coated materials
Prevention measures: Local extraction at source, proper welding helmet with respirator, regular air monitoring
The lesson: Some injuries don't show until decades later — but they're just as devastating.
Arc Flash Injuries
Scenario: Workers suffering eye damage and burns when basic or inadequate helmets fail to provide proper protection
Common failures: Outdated equipment, incorrect shade settings, insufficient face coverage
Prevention measures: Quality auto-darkening welding helmet, comprehensive PPE coverage, proper training
The lesson: Your eyes, face and skin deserve more than basic protection.
Noise-Induced Hearing Loss
Scenario: Multiple workers developing permanent hearing damage from prolonged exposure to welding and workshop noise
Common failures: Absence of hearing protection programs, unmonitored noise levels, extended exposure periods
Prevention measures: Noise assessment protocols, appropriate hearing protection, engineering noise controls
The lesson: You don't notice hearing damage until it's permanent.
The Ones You Never Hear About
If these types of incidents occur regularly in Australian workshops, how many close calls and quiet injuries never make the list? How many workers push through chest tightness from fume inhalation or get zapped by dodgy earth leads — and never say a word?
According to Safe Work Australia data, only about 60% of workplace injuries actually get reported. The rest? Swept under the rug. Pushed through. Ignored until they can't be anymore.
Think about that. For every welding injury that makes it into official statistics, there's likely another that disappeared into silence.
As experienced welding safety professionals often say during assessments, "The near-misses are your warning shots. Ignore them at your peril."
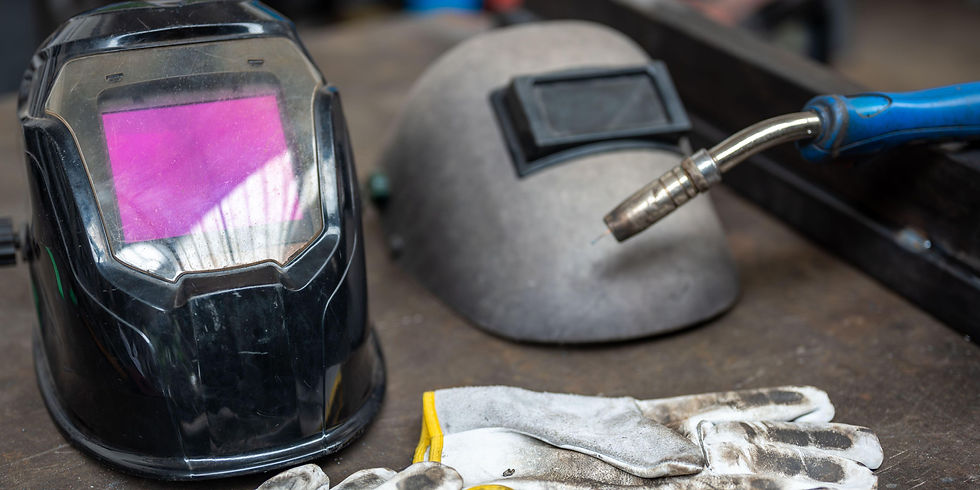
We Know What to Do — So Why Don't We Do It?
We've got the tech. The gear. The training. The WHS rules. But still — workshops cut corners. Why?
The Excuses That Kill
"We're behind schedule" — As if a deadline is worth a life
"This'll only take a minute" — The famous last words before disaster
"I've been doing it this way for 20 years" — Survival isn't the same as safety
"That gear costs too much" — Cheaper than a funeral
"It won't happen to me" — Said everyone it happened to
If you wouldn't weld blindfolded, why weld without a flashback arrestor? Why keep a cracked helmet? Why rely on your mate's home-brew ventilation setup?
The professionals who've spent decades with 3M Speedglas welding helmets on their heads will tell you — there's no project worth your eyesight. No deadline worth your lungs. No boss worth your life.
Wake Up Call: What Every Workshop Must Rethink About Weld and Safety
Invest in Prevention, Not Just Reaction
The old approach is waiting for the WorkSafe inspector to show up, then scrambling to make things right. That's not a safety strategy — it's a gamble with people's lives.
Prevention means:
Regular equipment audits (not just when something breaks)
Documented procedures that get FOLLOWED (not just filed)
Actual training (not just "watch Dave for a day")
Up-to-date equipment (not the same gear from 1995)
As safety experts demonstrate in their training materials, safety isn't about ticking boxes — it's about creating systems that make dangerous mistakes nearly impossible.
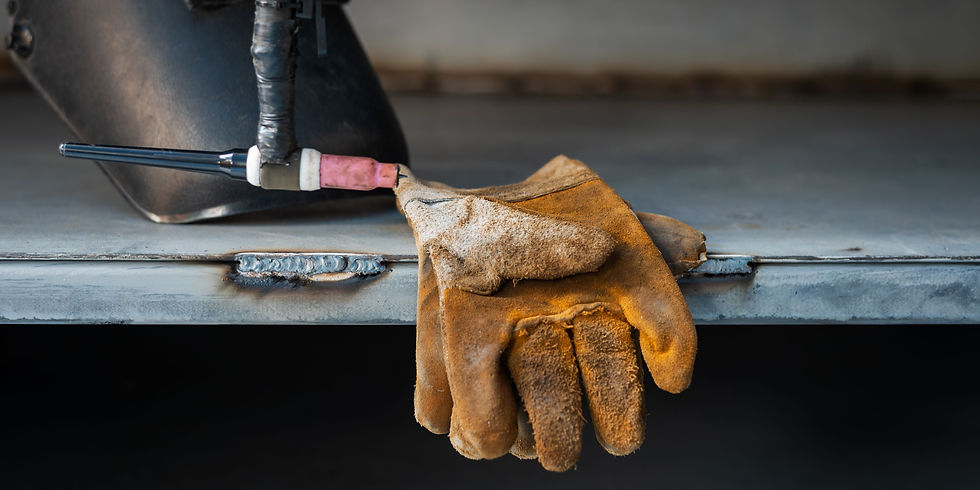
PPE Isn't Optional — It's Survival Gear
Your auto darkening welding helmet isn't a fashion statement. It's the difference between sight and blindness. That respirator isn't an accessory. It's the difference between healthy lungs and COPD.
Quality gear matters. There's a reason the professionals insist on proper equipment:
Speedglas helmets with proper optical ratings
Flame-resistant clothing that actually meets standards
Gloves that protect without sacrificing dexterity
Proper extraction systems that don't just move fumes around
Check out safety demonstrations comparing basic helmets to quality ones if you need convincing. The differences aren't just comfort — they're protection.
Do the Audit Before the Inspector Shows Up
Self-audits are uncomfortable. They force you to admit where you're falling short. But they're also the difference between being proactive and reactive.
Ask the hard questions:
Are all electrical connections properly maintained?
Are gas systems checked regularly for leaks?
Is ventilation adequate for the actual work being done?
Are all workers properly trained on safety procedures?
Are emergency protocols clear and practiced?
Industry safety resources regularly share worksheets for conducting your own safety audits. Use them. Before someone gets hurt.
Don't Store Fuel Like It's a Tin of Paint
Gas cylinder management is often the most overlooked aspect of welding safety. Yet it's one of the most dangerous when ignored.
Proper gas management means:
Securing cylinders so they can't fall
Separating oxygen from fuel gases
Installing and checking flashback arrestors
Proper storage away from heat sources
Regular inspection of hoses and connections
Safety experts emphasize this point repeatedly: respect the potential energy in those cylinders, because it doesn't care about your experience level when it explodes.
Respect Electricity — Or Regret It
Electricity follows the path of least resistance. Make sure that path isn't through you.
Electrical safety includes:
Proper grounding for both equipment and workpieces
Regular inspection of leads and connections
Using voltage reduction devices where appropriate
Keeping work areas dry
Understanding the risks of different welding processes
As shown in WeldConnect’s demonstrations, electrical safety isn't just about avoiding shock — it's about preventing fires, explosions, and equipment damage too.
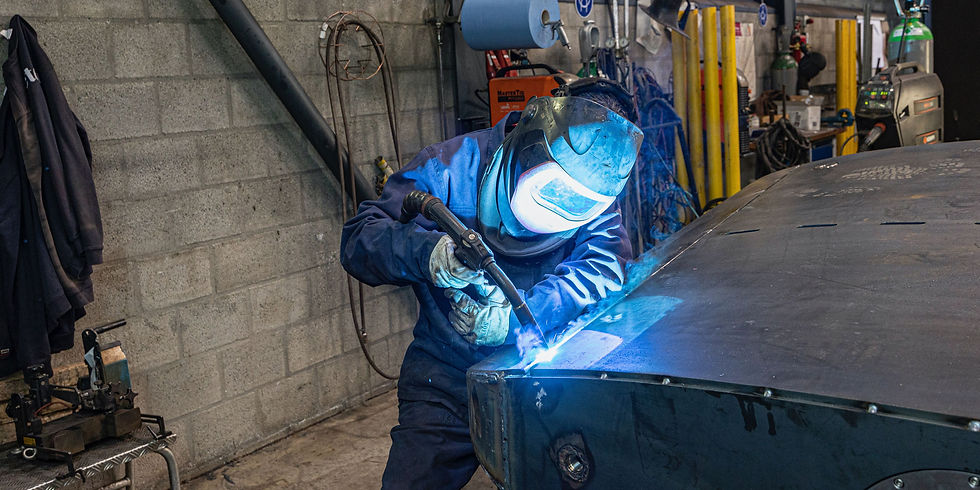
Weld and Safety Is a Choice You Make Every Day
Sam thought it wouldn't happen to him. Every injured worker does. So ask yourself — what are you waiting for? A close call? A tragedy? Or a wake-up call that never comes too late? Industry safety resources feature stories from real welders who've had these wake-up calls. Some were lucky enough to walk away and tell the tale. Others weren't.
Weld and safety isn't just jargon in an instruction manual. It's not just a training module you click through. It's the difference between going home to your family or not. Every time you pick up that torch, every time you strike that arc, you're making a choice. Make it the right one. Because Sam would give anything — literally anything — to go back and make a different choice that day. Don't wait until hindsight becomes your only teacher.
Comments