Weld and Safety Through Precision
- Jesse Tran
- May 28
- 6 min read
Updated: May 28

In Australian workshops from Kalgoorlie to Cairns, experienced welders know a hard truth: weld and safety isn't just about your helmet and gloves. It starts the moment you pick up your drill bit. Every year, structural failures trace back to the same culprit - not poor welding technique, but inadequate preparation work. A burr left on a drilled hole. A misaligned tap creating stress concentration. A rushed prep job using blunt tools.
Whether you're fabricating cattle yards in rural Queensland or high-rise steel in Sydney's CBD, the principle remains: true weld and safety begins with precision prep work using quality tools. Because when structural integrity is on the line, there's no such thing as "good enough" preparation.
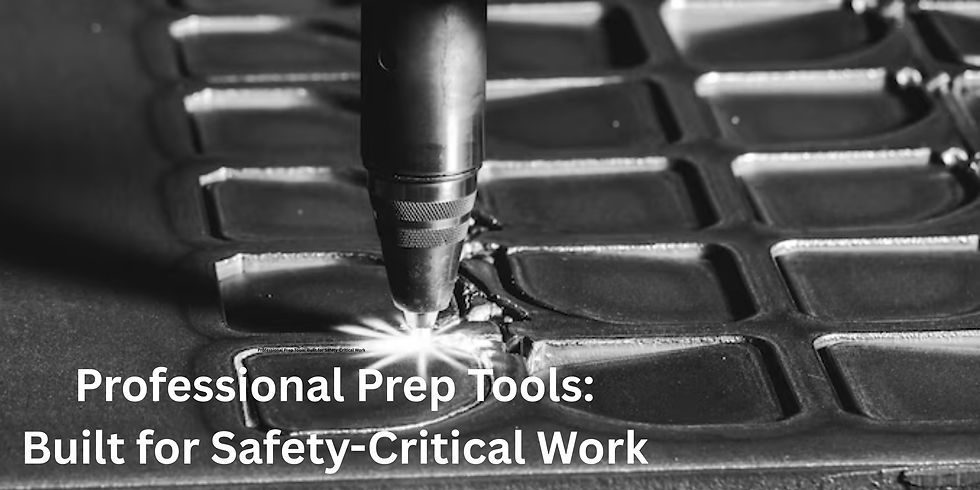
Why Weld and Safety Starts Before You Strike an Arc
After fifteen years inspecting workshops across Australia, I've seen the pattern countless times. The weld looks perfect from the outside - clean passes, good penetration, proper profile. But six months later, cracks appear. The hidden connection between prep work and structural safety runs deeper than most welders realise. AS/NZS 1554 doesn't just define welding procedures - it specifically outlines preparation requirements that directly impact long-term structural integrity.
I witnessed this during a Brisbane construction incident where a building frame connection failed. The investigation revealed that rough-drilled bolt holes had created stress risers that propagated fatigue cracks. The welds themselves were textbook perfect, but the preparation work had doomed the joint from day one. This is why precision equals safety in structural welding applications. Every burr, every misaligned hole becomes a potential failure point when loads start cycling through the structure.
The Critical Safety Risk Hidden in Poor Preparation
Drilling burrs create stress concentration points that amplify applied loads by factors of three or more. What should be uniform stress distribution becomes localised hot spots that initiate crack growth.
Tapping errors compound this problem: • Threads not cut straight create inconsistent bolt preload • Improper depth reduces thread engagement • Poor surface finish accelerates fatigue crack initiation
I've documented cases where material fatigue from poor prep created slow-motion disasters. A wind turbine foundation in South Australia failed after three years. Root cause analysis traced failure to inadequate hole preparation - rough drilling had created micro-cracks that grew under cyclic loading. The WHS implications are severe when prep work fails safety standards. WorkSafe investigations consistently find that preparation shortcuts contribute to structural failures endangering workers and the public.
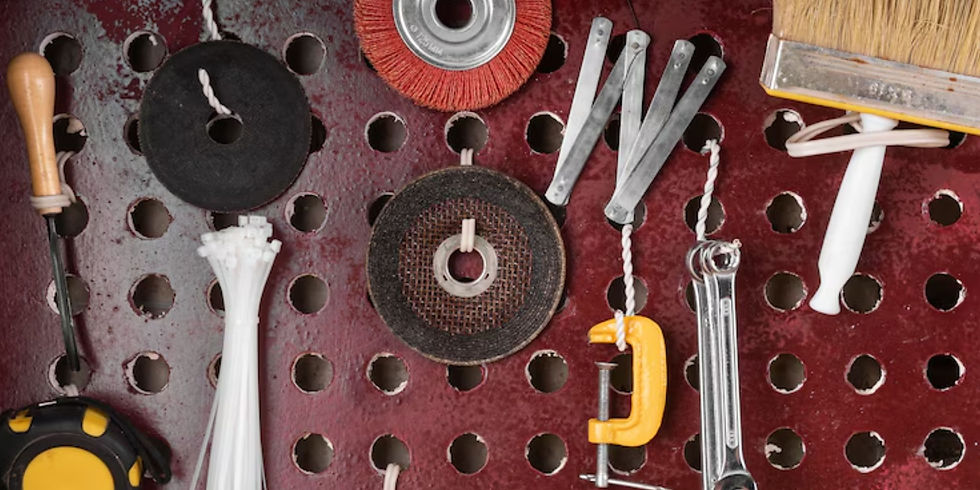
Precision Prep Tools: Your First Line of Safety Defense
Quality drills and taps aren't convenience tools - they're safety equipment. This mindset shift is crucial for Australian workshops operating under modern WHS requirements.
Material-specific requirements demand different approaches:
• Mild steel tolerates some roughness • Stainless steel requires quality welding supplies to avoid work hardening • Aluminium demands precise feeds to prevent material pickup
Tool precision directly impacts weld penetration and fusion. Oval holes from worn bits create gaps requiring excessive filler metal, leading to residual stress and distortion.
The safety cascade effect is real - poor prep tools force welders to compensate with technique modifications that move them outside qualified procedures. What starts as a $5 savings on a drill bit ends up compromising the entire weld specification. Australian workshop conditions amplify these challenges. Heat, dust, and humidity accelerate tool wear, while remote locations make tool failure a serious operational risk.
Quality Tools That Deliver Safety-Critical Precision
Professional-Grade Drill Bits
Drill bits welding applications require specific features: • Split-point geometry reduces walking and drilling forces • Cobalt alloy construction maintains sharpness in work-hardened materials • Step drills eliminate multiple tool changes while maintaining diameter control
Tap Selection for Structural Integrity
Proper tap sequence follows clear protocols:
Taper taps - Start threads in blind holes
Plug taps - Provide bulk of thread cutting
Bottoming taps - Complete threads to full depth
Using wrong tap sequence compromises thread engagement and joint strength.
Safety-Focused Tool Features
Tool design impacts operator safety: • Ergonomic designs reduce fatigue during extended operations • Proper chip evacuation prevents binding and breakage • Controlled cutting forces reduce workpiece movement risk
Tool failure recognition prevents accidents. Dull drills require excessive pressure, increasing breakage risk. Worn taps produce rough threads that won't achieve proper torque values.

Technique and Safety: The Human Factor in Precision
Safety protocols for drilling operations centre on speed, feed, and control. Excessive speed generates heat that work-hardens material and dulls tools. Insufficient feed allows tools to rub rather than cut.
Drilling Safety Steps:
Select appropriate speed for material and bit size
Use consistent feed pressure - let the tool cut
Clear chips regularly to prevent binding
Monitor cutting fluid application
Tap tools safety techniques emphasise straight threading and proper torque. Hand tapping requires feel to avoid breaking taps in blind holes. Power tapping demands torque-limiting equipment.
Tapping Safety Protocol:
Start tap square to workpiece surface
Back off every 2-3 turns to break chips
Use cutting fluid for consistent finish
Check thread engagement with gauges
Tool maintenance as safety practice means recognising when cutting performance degrades. Sharp tools require less force and operate predictably. Dull tools bind, break, and produce work compromising structural integrity.
Building a Safety-First Precision Culture
Experienced Australian welders invest in quality preparation tools because they understand the total cost equation. A $50 tap set producing consistent threads costs far less than a single rework job.
Workshop Protocol Development:
• Establish prep standards supporting qualified procedures • Create inspection checkpoints verifying preparation quality • Document preparation work with same rigour as welding records • Train operators on safety implications of poor prep
Mentoring young tradies requires teaching safety value of proper prep. Show them failed components. Explain how shortcuts led to structural problems. Make the connection between precision and professional responsibility explicit. Creating accountability systems ensures consistency across operators. When everyone understands preparation directly impacts structural safety, shortcuts become culturally unacceptable.
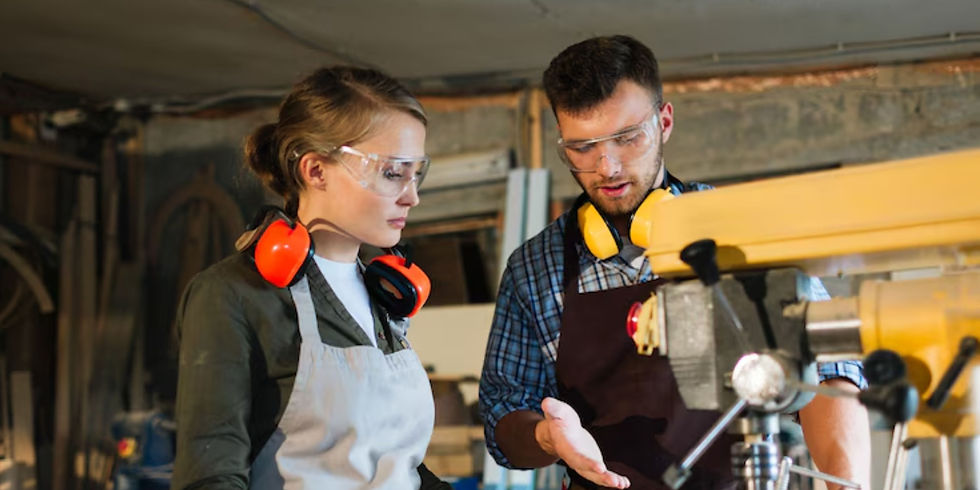
Professional-Grade Prep Equipment for Safety-Critical Work
Steel prep safety demands professional-grade equipment designed for Australian conditions. Tools maintaining accuracy under demanding workshop environments.
Essential Equipment Categories:
• Cutting fluids - Extend tool life while improving finish quality • Magnetic drill stands - Ensure consistent hole location and perpendicularity • Precision guides - Transform challenging operations into controlled processes • Complete prep kits - Material-specific tool selections eliminating guesswork
Tool storage and organisation systems support safety protocols by ensuring tools remain sharp and accessible. Proper storage prevents damage. Clear organisation reduces setup time and eliminates temptation to use inappropriate tools.

The Final Safety Check
Pre-weld inspection protocols should verify dimensional accuracy, surface finish, and thread engagement:
• Simple go/no-go gauges confirm hole diameters • Thread gauges verify tap quality and engagement length • Surface finish checks ensure weld procedure compatibility
Quality documentation requirements for safety-critical applications demand written records:
• Hole location verification data • Tool calibration records • Operator qualification currency • Material traceability documentation
The connection between prep precision and long-term structural integrity becomes clear when investigating failures. Investment thinking treats quality prep tools as safety infrastructure - essential equipment preventing problems.
Building reputation through consistent safety-focused precision distinguishes professional workshops from price-competitive operators. Clients recognise quality preparation work and the reduced risk it represents.
FAQs
How does drilling accuracy directly impact weld safety? Precise holes ensure consistent gap and land dimensions supporting qualified welding procedures. Rough or oversized holes require procedure modifications that may compromise structural integrity and introduce residual stress.
Can poor tapping compromise the safety of structural welds? Absolutely. Improperly cut threads prevent bolts from achieving specified preload, creating uneven load distribution across joint interfaces. This leads to fatigue problems and potential connection failure under service loads.
What makes a drill bit suitable for safety-critical applications? Professional drill bits feature precise point geometry, appropriate cutting angles for specific materials, and alloy construction maintaining sharpness. They produce consistent hole quality supporting structural welding requirements.
Which cutting fluids meet Australian safety standards for enclosed workshops? Water-soluble cutting fluids provide excellent lubrication while meeting workplace safety requirements for enclosed spaces. They reduce fire hazards while maintaining cutting performance and tool life in demanding applications.
When should prep tools be replaced to maintain safety standards? Replace tools when cutting performance degrades, hole quality becomes inconsistent, or excessive force is required for normal operations. Sharp tools are safer tools that produce work meeting structural requirements consistently.
Comments