Top 5 Myths About Flashback Arrestor Testing in Australia
- Mick Delaney
- May 15
- 5 min read

The Safety Reality Gap
You'd think by now, with decades of WHS regulations, TAFE training, and access to solid manufacturer guidance, the debate around flashback arrestor testing would be put to rest. But somehow, the myths persist.
From "you don't need to test them if they're still clicking" to "they last forever if you store them properly", the claims we hear floating around Aussie welding workshops and internet forums range from mildly misinformed to downright surreal. Even in professional settings, long-time tradies and apprentices alike are still picking up outdated or flat-out wrong advice about flashback arrestors — often from someone they trust who never got the memo themselves.
The internet hasn't helped either. With so many unverified videos, old manufacturer brochures, and half-baked opinions being recycled, it's no wonder there's confusion. But when you're dealing with live gas welding systems, the consequences of believing a myth aren't just regulatory — they're physical.
That's why we're writing this. To cut through the noise and close the chapter on these stubborn myths once and for all. Below, we break down the top 5 myths about flashback arrestor testing, why they're wrong, and what Australian Standards and real-world safety data actually say.
Common Misconceptions Debunked
Myth 1: Flashback Arrestors Last Forever
The Truth: Equipment Degradation Is Inevitable
No, they don't. Like all safety equipment, flashback arrestors degrade over time.
Australian Standard AS 4839:2011 recommends regular inspection and testing of flashback arrestors to ensure continued function. Internal seals, check valves and arresting components can all wear out—especially in high-use or rough environments. If you're still using arrestors from the early 2000s, you're gambling with risk.
Myth 2: If It Looks Fine, It Works Fine
The Truth: Hidden Dangers Within
Internal failure is invisible.
You can't tell if a flashback arrestor is working just by looking at it. Even if there are no dents, corrosion or wear, the check valve inside might be stuck open, or the arresting mesh might be compromised. Proper testing involves pressure, flow and ignition simulation—not a visual once-over.
Myth 3: Flashbacks Only Happen with Cheap Gear
The Truth: Quality Equipment Isn't Immune
Even high-end equipment is vulnerable to flashbacks.
Flashbacks result from incorrect gas flow, back pressure, hose leaks, or user error—not just poor equipment. Quality arrestors reduce the damage, but they're not invincible. Skipping testing just because you "buy the good stuff" is like refusing to service your ute because it's a Hilux.
Myth 4: Annual Testing Isn't Mandatory
The Truth: Standards & Liability Considerations
It may not be legally required in all cases—but it is the industry standard.
AS 4839:2011 sets the benchmark: flashback arrestors should be tested annually or according to manufacturer recommendations. Some workshops push that out to 2 years, but doing so increases liability. If you're ever audited or investigated post-incident, outdated or untested arrestors will be a red flag.
Myth 5: You Can Test Them Yourself
The Truth: Professional Testing Requirements
Flashback arrestor testing requires controlled pressure and reverse-flow simulation—this isn't a DIY task.
Testing must be done using calibrated equipment to confirm:
Leak tightness under pressure
Non-return valve operation
Flame arrest effectiveness
Improper testing setups can introduce risk, or give false reassurance. Leave it to qualified technicians.
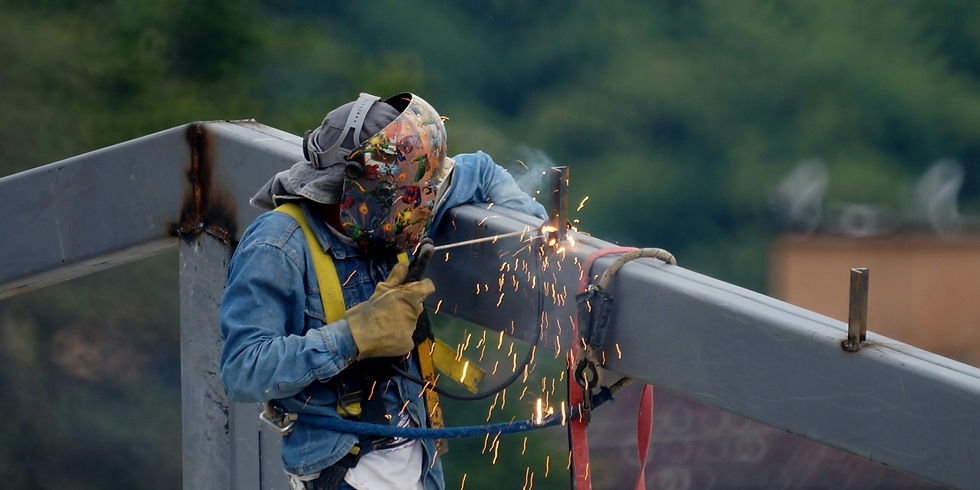
Professional Testing Solutions
Finding Qualified Testing Services
Even if you understand the risks, many Aussie workshops still aren't sure where or how to get their flashback arrestors tested properly—especially outside metro areas.
That's where trusted providers like WeldConnect come in.
Why Choose Professional Testing
WeldConnect is known across the Australian welding industry for its commitment to workshop safety, testing accuracy, and industry education. They don't just sell gear—they actively support compliance-driven services like:
Flashback arrestor testing (bench-certified)
Full inspection reports (for audit use)
On-site testing for multi-bay shops
Equipment traceability for WHS logs
Advice on compliance under AS 4839:2011
Whether you're a small rural shed or a major industrial operation, WeldConnect's team of welding safety professionals can help you test, prove, and document your flashback arrestors the right way.
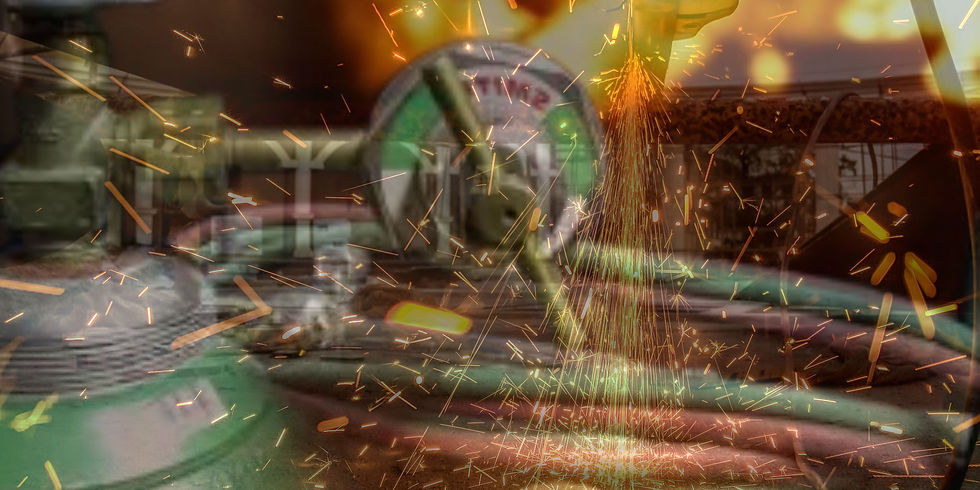
The Testing Process Explained
Specialised Equipment Required
Testing a flashback arrestor isn't just a matter of plugging it in and turning the gas on. Proper testing involves specialised equipment designed to measure leak tightness, pressure stability, and reverse flow protection under controlled conditions.
Essential Testing Equipment Components
Reverse Flow Testing Unit
Simulates incorrect flow direction to verify if the non-return valve activates correctly.
Leak Detection Equipment
Detects leaks under pressure using either bubble solution or electronic sniffers.
Flashback Simulation Tester
Confirms whether the arrestor will quench a flashback using safe ignition and flame arrest tests.
Pressure Regulators & Gauges
To simulate real-world conditions and ensure testing matches rated pressures.
Calibration & Traceability Labels
Essential for WHS audits and equipment logs.
Preparing for Professional Testing
Items You Should Have Ready
The flashback arrestor unit (clean and labelled)
Associated hoses or torch gear (if testing full assemblies)
Access to calibration or batch records (if applicable)
A record of last test date, if known
Important Safety Notice: Never attempt to perform these tests using makeshift setups or untrained personnel. Pressure testing involves risk and should always be handled by qualified technicians.
Industry Best Practices
For Workshop Managers
Regular testing isn't just about compliance—it's about protecting your team and equipment. Establish a testing schedule as part of your maintenance planning to avoid costly downtime and potential incidents.
For WHS Officers
Documentation is critical. Ensure all gas flow meter readings and flashback arrestor tests are properly recorded and stored for audit purposes. This creates a safety history that demonstrates due diligence.
For Rural & Remote Operations
Distance shouldn't compromise safety. Schedule batch testing during supplier visits or explore mobile testing options from certified providers who service regional areas.
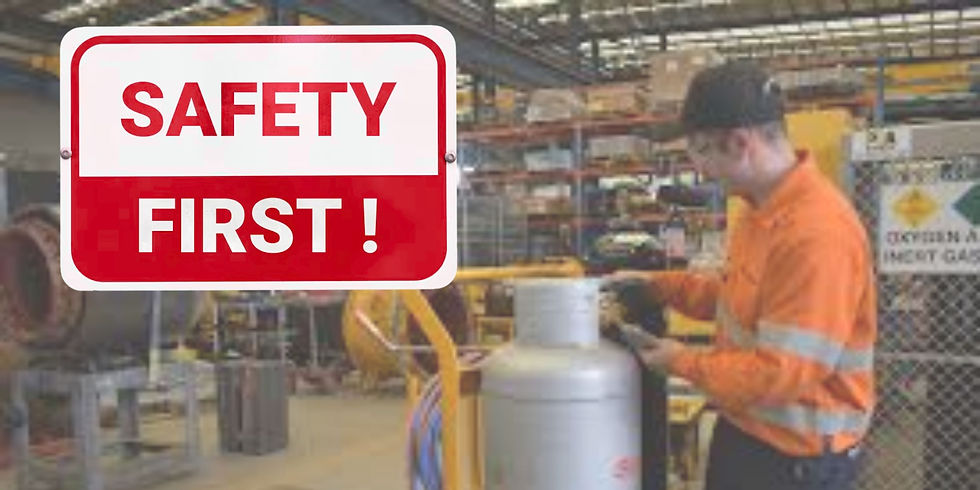
Safety Beyond Compliance
These myths have clung to the industry like spatter on steel, but it's time we grind them off for good. When it comes to flashback arrestor testing, there are no shortcuts worth taking.
If you're unsure whether your arrestors are up to scratch, don't gamble. Get them tested by pros like WeldConnect, update your compliance logs, and replace anything that doesn't meet spec. In a world where lives, gear, and liability are on the line, that's not just the smart move—it's the required one.
Frequently Asked Questions
Common Testing Queries
Q1: Do flashback arrestors really need to be tested regularly? Yes. AS 4839:2011 recommends flashback arrestors be tested annually or per manufacturer guidance to ensure full reverse flow and flame arrest functionality.
Q2: How do I know if my flashback arrestor is still working? Only proper pressure and reverse flow testing can confirm functionality. Physical appearance alone is not a reliable indicator of performance or safety.
Q3: Who can test flashback arrestors in Australia? Qualified safety suppliers like WeldConnect offer certified flashback arrestor testing using calibrated equipment, suitable for WHS and audit compliance.
Q4: Can flashback arrestors fail without warning? Yes. Damage, contamination, or worn seals can cause internal failure, making arrestors ineffective even if they look fine externally.
Q5: What's the risk of using an untested flashback arrestor? An untested arrestor may fail during a flashback event, leading to serious injury, equipment loss, or even fatal explosions.
Equipment Selection Guide
Q6: How do I choose the right flashback arrestor for my setup? Select arrestors rated for your specific gases and pressure ranges. Always choose models that comply with AS 4839:2011 and feature clear certification markings.
Q7: Is there a difference between flashback arrestors for different gases? Yes. Oxygen, acetylene, and other gases require specific arrestor types. Never interchange them between different gas applications as this creates serious safety risks.
Additional Resources
Australian Standards References
For workshop managers and safety officers seeking more information, the following standards provide comprehensive guidance:
AS 4839:2011 - The primary standard for flashback arrestor requirements
AS 4603 - Flash arrestors for welding equipment
AS 4289 - Oxygen and acetylene gas reticulation systems
Training & Support
Looking for team training on proper oxy acetylene equipment handling and safety? Professional development courses are available through certified TAFE providers and industry specialists.
Industry Partnerships
WeldConnect maintains relationships with leading oxy acetylene kit manufacturers to ensure testing procedures meet both Australian Standards and manufacturer specifications.
Comments