Streamlining Welding Operations with CEA Welding Machine
- Brock Smith
- Jun 11
- 6 min read
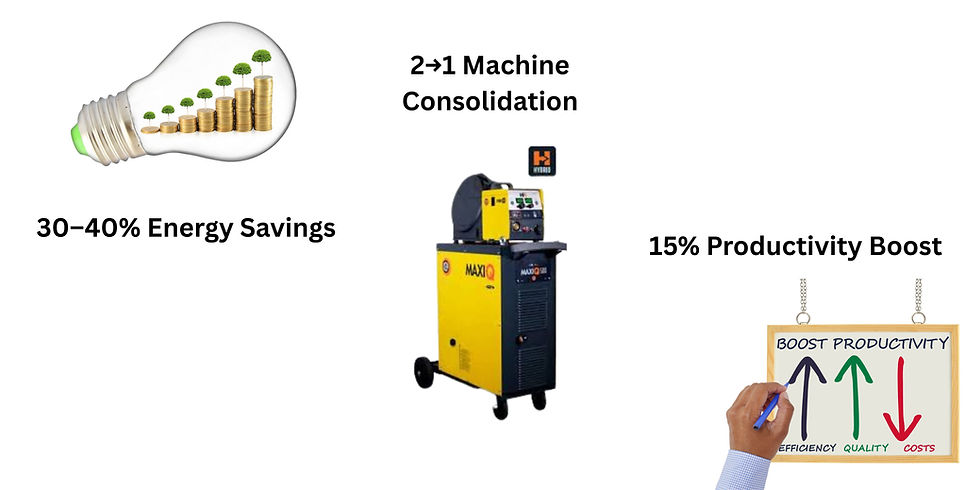
Did you know the average Australian welding workshop spends up to 30% more on electricity and maintenance costs because of outdated, multiple machines? Every minute your team spends switching between two different welders is productivity lost — and in a competitive industry, time is money. But what if one machine could do it all — faster, safer, and cleaner?
Modern CEA welding machines are designed to consolidate your workshop's equipment, cut energy use, and streamline operations without sacrificing quality or versatility. Whether you're running a busy Perth workshop or managing a regional fabricating team, upgrading to a reliable CEA welding machine could be the key to unlocking efficiency and compliance in one tidy package.

Why Are Multiple Old Welding Machines Costing You More?
Running multiple older welding units in your workshop creates a cascade of hidden costs that eat into your bottom line. The most immediate impact hits your power bill — older machines typically consume 40-60% more electricity than modern inverter-based units, especially when running continuously throughout the day.
Maintenance becomes a nightmare when you're juggling spare parts, service schedules, and repair costs across multiple machines. Each unit requires its own consumables, replacement parts, and regular servicing, which means more downtime and higher inventory costs. When one machine breaks down, your entire workflow can grind to a halt whilst you shuffle jobs between remaining units.
The workspace inefficiencies are equally problematic. Multiple machines mean multiple gas bottles, power leads snaking across the floor, and operators constantly moving between stations. This creates safety hazards, wastes valuable floor space, and slows down job completion times significantly.
What Makes CEA Welding Machines Different?
CEA welding machines represent a significant leap forward in welding technology, specifically engineered to handle multiple welding processes from a single unit. These multiprocess machines seamlessly switch between MIG, TIG, and stick welding modes, eliminating the need for separate dedicated machines.
The digital control systems are a game-changer for Australian workshops. Pre-programmed settings for common materials and thicknesses mean operators spend less time adjusting parameters and more time laying down quality welds. The inverter technology delivers precise arc control whilst dramatically reducing power consumption compared to traditional transformer-based machines.
Built to withstand Australia's harsh conditions, CEA machines feature robust construction with enhanced cooling systems and dust protection. The compact design means you can fit the equivalent of two or three older machines into the footprint of one unit, freeing up valuable workshop space for other equipment or additional work areas.
Whether you're searching for a CEA welding machine Perth workshop can rely on, these units deliver consistent performance across all welding processes whilst maintaining the reliability Australian tradies demand.
When One CEA Machine Does The Job of Two
Take the example of a regional fabrication workshop in Bunbury that recently upgraded from two separate MIG and TIG machines to a single CEA multiprocess unit. Within three months, they reported a 25% reduction in electricity costs and halved their consumables inventory requirements.
The space savings allowed them to install an additional workbench, increasing their capacity to handle smaller jobs alongside major fabrication projects. Productivity improved by approximately 15% as operators no longer needed to move between different machines or wait for equipment to become available.
A Perth-based automotive workshop experienced similar benefits after consolidating three older machines into one CEA unit. They eliminated two separate gas bottle setups, reduced their monthly equipment lease costs by $180, and saw a noticeable improvement in weld quality consistency across different processes.
The quantifiable benefits extend beyond immediate cost savings. Both workshops reported improved operator satisfaction due to simplified workflows and reduced physical strain from moving between multiple machines throughout the workday.
Space, Safety & Savings
Modern CEA welding machines contribute significantly to improved weld and safety standards in Australian workshops. Consolidated equipment means fewer power leads, reduced gas bottle requirements, and cleaner workspace layouts that comply with workplace safety regulations.
The advanced fume extraction compatibility and reduced electromagnetic interference create a healthier working environment. Operators report less fatigue and improved concentration when working with quieter, more efficient equipment that produces consistent results.
Power bill savings compound over time, with many workshops seeing 30-40% reductions in welding-related electricity costs. The inverter technology draws power more efficiently, and standby power consumption is minimal compared to older transformer-based machines that consume power continuously.
Simplified inventory management becomes a major advantage when you're dealing with one machine instead of multiple units. Single-source consumables, standardised replacement parts, and unified service schedules reduce administrative overhead and minimise the risk of running out of critical components.
How to Decide If Your Workshop Is Ready for a CEA Welding Machine Upgrade
Several clear indicators suggest your workshop would benefit from upgrading to a CEA welding machine:
Power costs are climbing — If your electricity bills show welding equipment consuming disproportionate amounts of power, especially during lighter work periods
Maintenance schedules overlap — When you're constantly servicing different machines or struggling to source parts for older units
Space constraints limit growth — Multiple machines prevent you from expanding capabilities or taking on larger projects
Operator complaints increase — Staff report difficulty switching between different control systems or waiting for equipment availability
Quality inconsistency emerges — Different machines produce varying weld quality, affecting your reputation or requiring rework
Additionally, if you're running machines over seven years old, the technology gap likely justifies an upgrade purely on efficiency and safety grounds.
Choosing the Right CEA Welding Machine for Your Needs
Selecting the appropriate CEA machine requires careful consideration of your workshop's specific requirements. Process capability should match your current and anticipated future needs — ensure the unit handles the welding processes you use most frequently with adequate amperage ranges.
Power requirements must align with your electrical infrastructure. Single-phase units suit smaller workshops, whilst three-phase machines provide better performance for high-demand applications. Consider both input power availability and running costs when making this decision.
Portability becomes crucial if you service multiple sites or need flexibility in machine positioning. Some CEA units feature wheeled bases or compact designs that facilitate easy movement between work areas.
When sourcing quality welding supplies and CEA equipment, prioritise suppliers offering comprehensive technical support, readily available spare parts, and established service networks across Australia. Local support significantly impacts long-term ownership costs and minimises downtime when issues arise.
Training & Maintenance
Successful implementation begins with proper operator training. Even experienced welders benefit from familiarisation sessions covering digital controls, process switching procedures, and optimal parameter settings for common applications.
Schedule initial training during lighter work periods to allow operators time to practice without production pressure. Focus on the differences between old and new systems, emphasising the advanced features that improve efficiency and quality.
Establish routine maintenance protocols from day one. CEA machines require different maintenance approaches compared to older equipment, particularly regarding software updates, cooling system cleaning, and electronic component care.
Implement safety audits that reflect the new equipment configuration. Update your workshop safety procedures to account for consolidated equipment layouts and modified workflows. Ensure emergency procedures address the multiprocess capabilities and any new safety features.
Parts management becomes simpler but requires adjustment to new consumables and replacement components. Establish relationships with suppliers early and maintain adequate stock levels of essential consumables to prevent workflow disruptions.

Starts with the Right Welding Machine
The evidence is clear — modern CEA welding machines offer compelling advantages over maintaining multiple older units. From substantial electricity savings and reduced maintenance costs to improved safety and workspace efficiency, the benefits extend far beyond simple equipment consolidation.
Australian workshops that have made the transition consistently report improved productivity, better weld quality, and enhanced operator satisfaction. The space savings alone often justify the upgrade, whilst ongoing operational cost reductions provide long-term financial benefits.
If your workshop is struggling with multiple older machines, rising power costs, or space constraints, a CEA welding machine upgrade deserves serious consideration. The technology has matured to the point where reliability and performance exceed traditional equipment whilst delivering measurable efficiency improvements.
Ready to streamline your welding operations? Contact your local welding equipment specialist to discuss how a CEA welding machine could transform your workshop's productivity and profitability.
FAQs
Can a single CEA welding machine really match the output of two separate machines?
Yes, modern CEA multiprocess machines are designed to handle the workload of multiple dedicated units. With rapid process switching and consistent high-performance output, they often exceed the combined productivity of older separate machines by eliminating transition time and maintaining optimal arc characteristics across all welding modes.
How much can I expect to save on electricity bills with a CEA welding machine?
Australian workshops typically see 30-40% reductions in welding-related electricity costs after upgrading to CEA machines. The exact savings depend on your current equipment age, usage patterns, and local electricity rates, but most workshops recover the power efficiency investment within 12-18 months.
What happens if my CEA machine breaks down — am I left with no welding capability?
Quality CEA machines are built for reliability and often feature diagnostic systems that prevent major failures. However, reputable suppliers offer rapid service response, loan machines, and comprehensive warranty coverage. Many workshops find single-machine reliability superior to managing multiple older units prone to unexpected breakdowns.
Are CEA welding machines suitable for heavy-duty industrial applications?
Absolutely. CEA machines are engineered for continuous industrial use and often exceed the duty cycles of older equipment. The inverter technology provides more stable arcs under demanding conditions, whilst advanced cooling systems ensure consistent performance during extended welding sessions.
How difficult is it to train operators on CEA welding machines?
Most experienced welders adapt to CEA machines quickly due to intuitive digital controls and familiar welding processes. The learning curve typically involves understanding the digital interface and process switching procedures rather than relearning welding techniques. Comprehensive training usually takes 1-2 days for full proficiency.
댓글