Replacing Welding Testing Machines vs. Visual Checks
- Sophie Williams
- May 12
- 6 min read

Dave Mitchell, a workshop supervisor at Eastern Coast Fabrication, prided himself on his routine visual inspections. Twice a week, he meticulously checked cables, connections, and components. It was a system that had served him well for years. But one afternoon, after a visual check on a MIG welder, disaster struck. The machine failed catastrophically during use, sending an apprentice scrambling with singed gloves and a terrified expression. This scenario isn’t unique.
Many Australian workshops rely heavily on visual inspections, but what’s visible isn’t always the full story. Internal faults, like electrical failures or gas leaks, can remain undetected by the human eye, and these invisible issues can lead to catastrophic failures. Welding machine testing using specialized equipment—like flashback arrestor testers and crack detection kits—isn’t just a precaution; it’s essential for safety and compliance. In this article, we’ll explore why relying on visual checks alone is no longer enough in today’s high-risk welding environments.
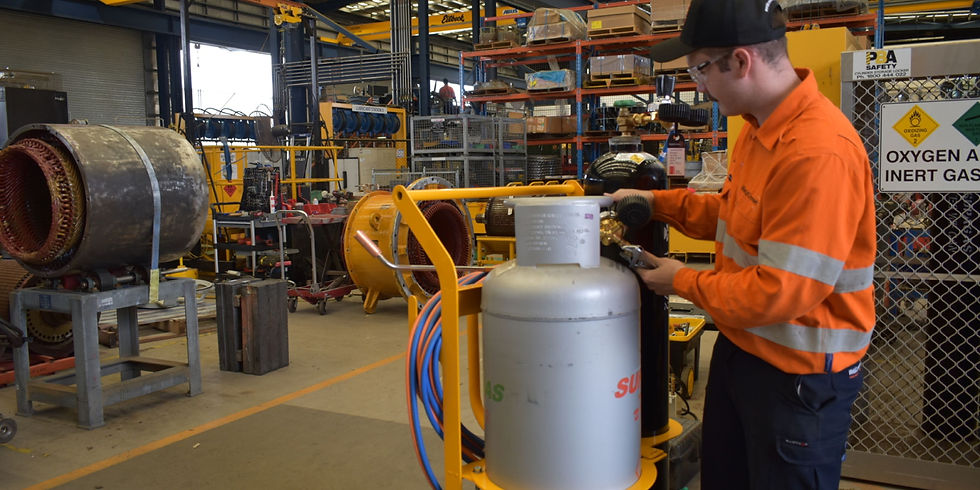
The Hidden Dangers of Visual-Only Inspections
The Limitations of What We Can See
Visual inspections certainly have their place in workshop safety protocols. A seasoned welder can spot obvious signs of wear, damage, or misalignment. These checks might include:
Examining cables for external damage or wear
Checking gas hoses for visible cracks or deterioration
Inspecting torch components for damage or blockages
Looking for loose connections or fittings
However, the most dangerous faults often remain invisible to the naked eye. Internal electrical issues, microscopic cracks in critical components, and partial blockages in gas systems can all escape detection during even the most diligent visual assessment.
Real Consequences of Missed Detections
The consequences of these invisible failures can be severe and immediate:
Case Study: Melbourne Fabrication Workshop, 2023A seemingly well-maintained MIG welder passed multiple visual inspections but experienced a catastrophic electrical failure due to internal insulation breakdown. The resulting electrical arc caused severe burns to the operator and triggered a workshop fire that caused $75,000 in damage and weeks of downtime.
The investigation revealed that proper electrical testing would have identified the degrading insulation long before it reached critical failure.
When Australian Standards Demand More
For workshops operating under Australian regulations, visual inspections alone don't satisfy compliance requirements. Key standards including:
AS/NZS 1674.1:2007 Safety in welding and allied processes
AS/NZS 1337.1:2010 Personal eye protection
AS/NZS 60974.1:2020 Arc welding equipment
All specify testing regimes that go well beyond what can be achieved through visual assessment. Non-compliance doesn't just risk safety—it can result in significant penalties, insurance issues, and potential liability in the event of accidents.
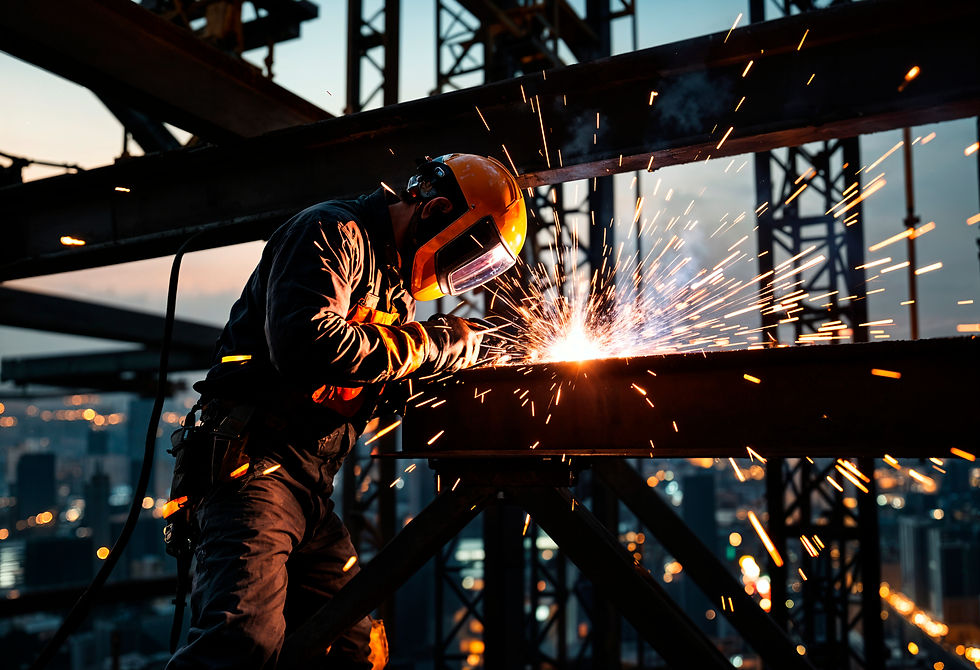
Understanding Essential Testing Equipment
Modern testing equipment provides objective, measurable data that confirms equipment functionality across multiple parameters. Let's explore the essential testing devices that should be part of every Australian workshop's safety protocol:
Electrical Safety Testers
Electrical safety testers verify that welding equipment operates within safe electrical parameters, checking:
Insulation resistance
Earth continuity
Circuit integrity
Leakage current levels
These specialized devices detect potential electrical hazards long before they cause accidents or equipment failure, providing quantifiable results that meet Australian Standards requirements.
Voltage Reduction Device (VRD) Testing
VRD in welding represents a critical safety feature designed to reduce shock hazards by automatically lowering the output voltage when the welding machine is not in use. However, these safety systems can fail without showing any external signs.
A VRD welding system that appears operational might actually have failed in its safety function. Only through proper testing with a calibrated VRD tester can you verify that these crucial safety systems function correctly when needed most. The test confirms:
Proper voltage reduction when idle
Appropriate response time
Consistent performance across operating conditions
Gas Equipment Safety Testing
One of the most dangerous failures in welding operations involves gas equipment. A flashback arrestor tester provides objective confirmation that these critical safety devices function properly by:
Verifying non-return valve functionality
Testing pressure-sensitive cut-off mechanisms
Confirming gas flow restrictions operate correctly
Checking for internal contamination that visual inspection cannot detect
Without proper testing, flashback arrestors might appear perfectly functional while actually failing to provide protection against potentially explosive gas flashbacks.
Crack and Defect Detection Systems
Modern crack detection kits use technologies including:
Dye penetrant testing
Magnetic particle inspection
Ultrasonic testing
These methods reveal microscopic cracks and structural weaknesses that visual inspection simply cannot detect. For critical components where failure isn't an option, these testing methods provide essential verification of structural integrity.

The True Cost of Inadequate Testing
Financial Implications Beyond Equipment Costs
While investing in testing equipment requires upfront expenditure, the financial mathematics clearly favor proper testing when considering:
Direct Costs of Equipment Failure
Emergency equipment replacement
Workshop downtime
Lost production
Repair costs beyond just the failed component
Indirect Financial Impacts
Insurance premium increases
Workers' compensation claims
Potential legal liability
Compliance penalties
Real-World Example: Perth Mining Services CompanyAfter implementing comprehensive testing protocols using professional equipment rather than relying on visual checks, a Perth-based mining services provider documented a 78% reduction in unexpected equipment failures over 18 months, generating estimated savings of $120,000 annually through reduced downtime alone.
Human Cost Considerations
Beyond financial impacts, equipment failures can result in serious injuries or worse. Australian Safe Work data indicates that electrical accidents and gas-related incidents in welding operations account for approximately 8% of all serious workshop injuries, with inadequate equipment testing identified as a contributing factor in over 60% of these cases.
Implementation: Creating an Effective Testing Protocol
Converting from visual-only inspections to a comprehensive testing protocol requires strategic planning:
1. Equipment Assessment and Selection
Each workshop's needs will vary based on:
Types of welding equipment used
Volume of equipment requiring testing
Operational environment (remote sites may need portable solutions)
Budget constraints
Key factors to consider when selecting testing equipment include:
Australian Standards compliance certifications
Calibration requirements and processes
Durability for workshop environments
Ease of use for staff conducting tests
2. Staff Training Requirements
Testing equipment is only as effective as the personnel operating it. Training considerations should include:
Initial certification training
Refresher courses on updated standards
Documentation protocols for test results
Interpretation of test data and escalation procedures
Staff should understand not just how to operate the equipment, but why each test matters and what the results indicate about equipment condition.
3. Testing Frequency Guidelines
Australian Standards provide minimum testing frequencies, but best practices often exceed these requirements:
Equipment Type | Australian Standard Minimum | Recommended Frequency |
Welding Power Sources | Annual | Quarterly |
VRD Systems | Annual | Quarterly |
Flashback Arrestors | 6-monthly | Quarterly |
Gas Regulators | Annual | 6-monthly |
Earth Clamps & Leads | 3-monthly | Monthly |
High-usage environments or harsh conditions may warrant even more frequent testing.
4. Record-Keeping Systems
Comprehensive record-keeping is essential for both compliance and equipment management:
Digital test records with standardized formats
Equipment-specific testing histories
Trend analysis to predict potential failures
Maintenance scheduling based on test results
Modern testing equipment often interfaces with digital record systems, streamlining documentation processes.
Case Studies: Testing Equipment in Action
Regional Queensland Fabrication Workshop
A medium-sized fabrication operation in regional Queensland implemented comprehensive testing protocols after a near-miss incident revealed undetected issues in seemingly functional equipment.
Challenge: Staff initially resisted the change, viewing visual checks as adequate based on years of experience.
Solution: Management implemented a phased approach, beginning with demonstration testing on equipment that had passed visual inspection. The results revealed numerous hidden issues, convincing even skeptical staff of the value.
Results:
17 potentially serious equipment faults identified in the first round of testing
92% reduction in unplanned equipment downtime
Insurance premium reduction of 15% after documenting improved safety protocols
Remote Mining Service Provider
A mobile welding service supporting remote Western Australian mining operations faced unique challenges implementing testing protocols across distributed sites.
Challenge: Testing equipment needed to be portable, durable, and operational in harsh conditions while maintaining accuracy.
Solution: Investment in ruggedized, portable testing equipment with self-calibration capabilities, combined with comprehensive staff training.
Results:
100% compliance with client site safety requirements
Competitive advantage in tendering processes
Zero lost-time incidents related to equipment failure over a 24-month period
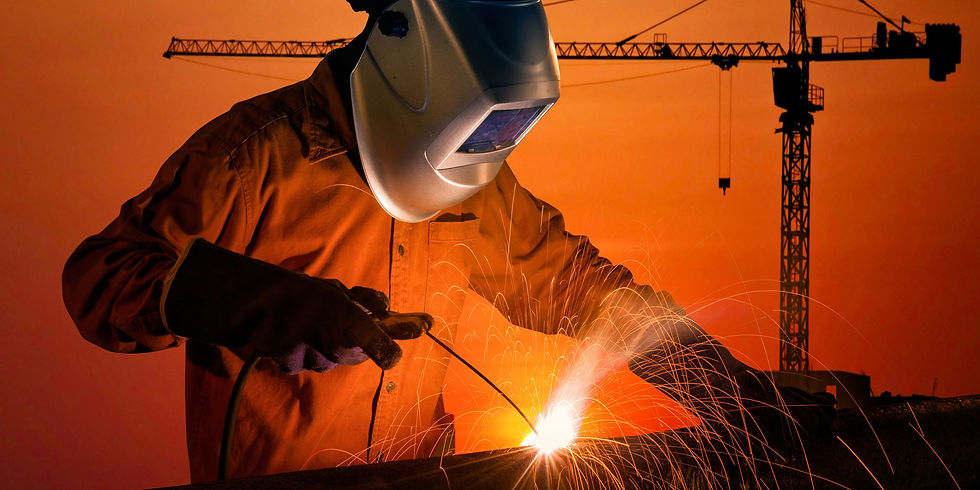
The Business Case for Professional Testing
The evidence clearly demonstrates that while visual inspections have their place, they cannot replace proper equipment testing. For Australian workshop supervisors and safety managers, the question isn't whether you can afford testing equipment—it's whether you can afford to operate without it.
Professional testing equipment provides:
Objective, measurable data on equipment condition
Documentation for compliance requirements
Early detection of potential failures before they become dangerous
Enhanced operator confidence in equipment safety
In an industry where equipment reliability directly impacts both safety and productivity, professional testing represents not just best practice but essential business intelligence. By identifying issues before they become failures, workshops can optimize maintenance schedules, extend equipment lifespans, and most importantly, ensure every worker goes home safely at the end of each shift.
As Australian Standards continue to evolve and workplace safety expectations increase, the gap between visual inspection and proper testing will only widen. Forward-thinking workshop managers are making the investment now, recognizing that professional testing is no longer optional—it's fundamental to responsible operation.
Comments